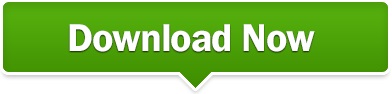
- DMG ADDITIVE MANUFACTURING FULL
- DMG ADDITIVE MANUFACTURING SOFTWARE
- DMG ADDITIVE MANUFACTURING SERIES
Minor modifications can be made without retrograde steps and with the same user convenience directly on the machine control.Īt the control level, CELOS SLM offers an adaptive exposure strategy that is automatically generated before the process starts. The tailored and standardised user interface can be used to program components – irrespective of their complexity – with minimum outlay and transfer the data immediately to the machine.
DMG ADDITIVE MANUFACTURING SOFTWARE
Holistic software solution for the powder bed methodĭMG MORI is also offering a comprehensive software solution with CELOS SLM for CAM programming and machine control in one package and with a standardised user interface. When the completed workpiece is released from the powder bed, any excess powder falls through a mesh into a container for reuse. This process is repeated until the component has been fully built.

Once all positions in one layer have been processed, the platform lowers according to the required layer thickness (between 20 and 100 μm). A continuous laser beam then melts the applied powder at the programmed positions in a cycle time of 10 μs.
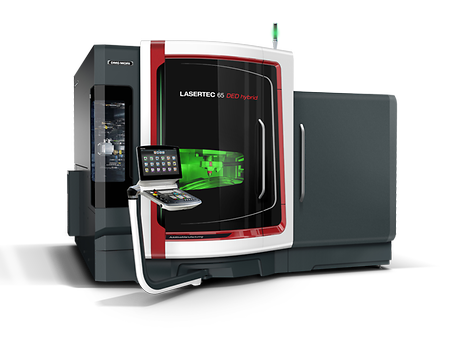
In the powder bed method, a thin layer of powder is applied to a lowering platform. The LASERTEC SLM machines are the current highlight. LASERTEC SLM: Revolutionary powder machine
DMG ADDITIVE MANUFACTURING FULL
As additive team players, these two innovations combined with high-tech machines in the DMG MORI machining portfolio offer numerous options for full industrial processing.
DMG ADDITIVE MANUFACTURING SERIES
While the LASERTEC 65 3D has been designed for pure laser deposition welding of larger parts, the LASERTEC SLM series has expanded the product range for the powder bed method using selective laser melting. Additive team player for the manufacturing industryĭMG MORI has now uniquely upgraded its portfolio with these LASERTEC 3D hybrid machines, developing a complete range for additive manufacturing. Both machines are designed for manufacturing comparatively large parts such as complex turbine components. This concept is used both in the LASERTEC 65 3D hybrid with additional 5-axis milling and in the LASERTEC 4300 3D hybrid combining laser deposition welding and 6-axis turning/milling. LASERTEC 3D hybrid: Finished part quality in one setupĭMG MORI successfully entered the market four years ago with machines in the LASERTEC 3D hybrid series, which combine laser deposition welding and subtractive machining. These methods have three continuous process chains, each based on machine technology and software, for powder bed and powder nozzle respectively. With regard to systems, DMG MORI offers customers from one source two of the most significant current additive manufacturing methods for metal components.

The starting point for this additive revolution is an extremely fine powder material with grain diameters of just a few μm. What also became clear when walking through the fair halls: as one of just a few manufacturers in this field, DMG MORI presented visitors with a large spectrum of options for further expansion of additive manufacturing.Īs an additive pioneer, the company used integrated process chains to show manufacturers its process competence with both powder bed and powder nozzle technology. Various providers exhibited new machines and concepts at the fair in Frankfurt, in particular trendsetting machines and exhibits for future manufacturing. The future is almost within reach – also thanks to DMG MORI! If there were any questions whether additive manufacturing in the metal sector could achieve the leap into industrial implementation, any doubts were answered at Formnext in November 2017.
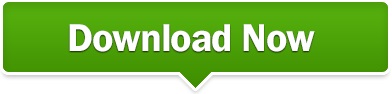